Blog
We regularly update articles related to the prototyping and manufacturing industry. You’re welcome to check our previous blogs and subscribe to our newsletter.
Transforming Metal Injection Molding: The Innovative Louis Machine
Metal Injection Molding (MIM) is a sophisticated manufacturing technique that blends powdered metal with a polymer binder to create intricate metal components. Its applications span industries, from aerospace to healthcare, offering cost-effective solutions for complex parts. Enter the Louis Machine, a pioneering advancement in MIM technology, poised to elevate precision and efficiency in metal component production.
What Is Metal Injection Molding (MIM)
Definition and MIM Process
Metal Injection Molding (MIM) is a specialized manufacturing process that seamlessly combines the precision of injection molding with the adaptability of metal materials. It commences with the formulation of a feedstock, a blend of finely powdered metal particles intricately mixed with a polymer binder. This concoction undergoes heating, resulting in a viscous compound primed for injection into molds, akin to the conventional plastic injection molding process.
Subsequently, the injected material goes through a debinding phase, meticulously eliminating the polymer binder. What remains is referred to as a “green” part. To culminate the process, the green part undergoes sintering at elevated temperatures, enabling the fusion of metal particles, ultimately yielding a dense metal component characterized by outstanding precision and mechanical attributes.
Applications and Benefits of MIM
MIM is celebrated for its adaptability, rendering it suitable for an extensive array of industries and purposes. From aerospace and medical devices to electronics and automotive components, MIM offers a multitude of merits:
- Complex Geometries: MIM excels in fabricating intricate and multifaceted parts with pinpoint precision, a feat often unattainable through conventional manufacturing techniques.
- Material Versatility: MIM accommodates a broad spectrum of metals, encompassing stainless steel, titanium, and even exotic alloys. This versatility permits the tailoring of material properties to fulfill specific requirements.
- Cost Efficiency: MIM curbs material wastage, constituting a cost-effective solution for the production of small, intricate metal parts.
- Minimal Post-Processing: Components produced through MIM typically necessitate minimal post-production efforts, resulting in time and resource savings.
The Ascendant Role of MIM in Manufacturing
In recent years, the prominence of MIM in manufacturing has experienced a steady ascent. As industries seek increasingly compact, precise, and intricate components, MIM has emerged as the preferred choice owing to its capacity to efficiently meet these demands. Its cost-effectiveness and adaptability have elevated it to a pivotal position across various sectors, contributing substantially to technological advancement and product innovation.
The Louis Machine Unveiled
Genesis and Development of the Louis Machine
The Louis Machine signifies a profound leap in Metal Injection Molding technology. Conceived and cultivated by a professional machining company boasting comprehensive expertise in precision mold design, plastic injection molding, metal hardware parts processing, and automotive parts manufacturing, the Louis Machine has undergone evolution to address the evolving demands of the industry.
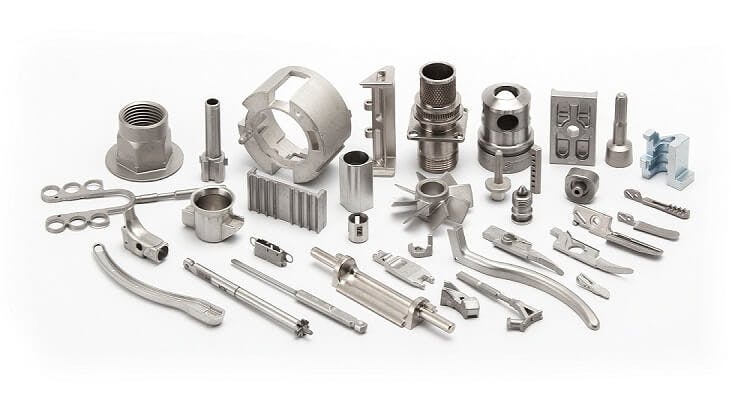
The machining company, with many years of experience behind it, is acutely aware of the potential to adapt MIM processes to contemporary manufacturing requirements. Their visions merged to create a machine. Designed to optimize the entire MIM workflow, from material preparation to final part production.
Key Features and Proficiencies
The Louis Machine distinguishes itself through an array of pivotal features and competencies:
- Heightened Precision: Infused with advanced control systems and precision engineering, the Louis Machine attains unparalleled levels of accuracy in the creation of MIM parts, ensuring uniformity and exceptional quality.
- Enhanced Efficiency: The Louis Machine streamlines the MIM process, curtailing cycle times and minimizing material wastage, thereby augmenting productivity and reducing operational costs.
- Material Dexterity: Exhibiting remarkable versatility, the Louis Machine adeptly handles an extensive spectrum of metal materials, rendering it an asset across diverse industries and applications.
- Automation Prowess: Automation functionalities alleviate the need for extensive manual labor, bolstering efficiency while mitigating human errors.
The Louis Machine’s Distinctive Industry Presence
The impact of the Louis Machine on the Metal Injection Molding domain is unequivocal. Its capacity to fabricate intricately detailed, precise, and cost-efficient metal components has revolutionized manufacturing for global enterprises. By pushing the boundaries of what is possible with MIM. Louis Machine has become a catalyst for innovation and operational efficiency, opening up new vistas in every sector. and promote the continued expansion of metal injection molding.
Impact of the Louis Machine on Metal Injection Molding
Enhanced Precision and Quality
The Louis Machine’s influence on Metal Injection Molding (MIM) is underscored by its capacity to elevate precision and quality standards to unprecedented levels. In the realm of manufacturing, precision is paramount. Products are processed with a state-of-the-art CNC milling machine, enabling the attainment of complex 3D curved surfaces with exceptional accuracy. Surface texture and hardness are meticulously fine-tuned, demanding a combined machining accuracy of ±0.002mm.
Further enhancing precision, Varo precision mold parts exhibit remarkable accuracy in EDM (Electrical Discharge Machining), achieving tolerances as tight as ±0.003mm while maintaining an exceptionally uniform surface hardness. Grinding processes on the Louis Machine maintain accuracy within ±0.002mm, contributing to the overall quality and precision of MIM components. This heightened level of precision ensures that Louis Machine-produced parts consistently meet exacting specifications, driving excellence in product manufacturing.
Increased Efficiency and Productivity
Efficiency is a cornerstone of the Louis Machine’s impact on MIM. By streamlining the MIM process, this advanced technology significantly reduces cycle times and minimizes material waste. This greatly improves overall efficiency. Manufacturing processes that once required a lot of manual labor can now be automated. Further improve productivity and reduce the possibility of human error. This newfound efficiency doesn’t just speed up production. It also helps save costs, making MIM a more economically viable option for many industries.
Cost-Saving Benefits
The Louis Machine’s influence on MIM extends to its cost-saving benefits. By reducing material wastage, optimizing production processes, and automating tasks, manufacturers can significantly reduce operational costs. This cost-effectiveness is particularly beneficial for the production of small, intricate metal components, where traditional manufacturing methods may prove less economical. Additionally, the ability to achieve high precision and quality standards without excessive post-processing further contributes to cost savings.
The Future of Metal Injection Molding with the Louis Machine
Potential Innovations and Advancements
The Louis Machine hints at a promising future for Metal Injection Molding, ripe with potential innovations and advancements. As technology continues to evolve, the machine is likely to undergo further enhancements, pushing the boundaries of what is achievable in terms of precision, material versatility, and automation.
Anticipated Market Trends and Growth
In the coming years, Metal Injection Molding is poised to experience substantial growth. As industries increasingly demand compact, intricate, and high-precision components, MIM is well-positioned to meet these requirements efficiently. The market for MIM applications, spanning aerospace, medical, automotive, and more, is expected to expand as the technology becomes more accessible and cost-effective. The Louis Machine, with its ability to enhance efficiency and quality, is likely to play a pivotal role in driving this growth.
Prospects for Widespread Adoption
The prospects for widespread adoption of the Louis Machine in Metal Injection Molding are promising. It optimizes the entire MIM workflow from material preparation to final part production. Making it a valuable asset for manufacturers in different industries. As awareness of their capabilities continues to increase, and manufacturers seek to remain competitive by producing high-quality, precise parts. The Lewis machine is likely to become an indispensable tool in manufacturing. Its impact is expected to transcend individual companies and shape the future of MIM as a whole. Unleashing new possibilities in metal parts production.
Embrace the Future of Manufacturing with the Louis Machine: Explore Precision, Efficiency, and Savings in Metal Injection Molding (MIM)
In conclusion, the innovative Louis Machine has emerged as a transformative force in Metal Injection Molding (MIM). With its unmatched precision, enhanced efficiency, and cost-saving benefits, it promises to reshape the landscape of metal component production. As we look to the future, the Louis Machine’s potential for driving innovation, anticipating market trends, and facilitating widespread adoption underscores its pivotal role in advancing MIM technology and ensuring its continued growth and success in manufacturing industries worldwide.