Blog
We regularly update articles related to the prototyping and manufacturing industry. You’re welcome to check our previous blogs and subscribe to our newsletter.
Custom Metal Forging Service: A Comprehensive Guide
Custom metal forging is a vital manufacturing process that shapes metal using compressive forces. This blog explores various aspects of custom metal forging, highlighting its benefits across different industries, the process involved, and tips for choosing the right service provider like Louis Machine.
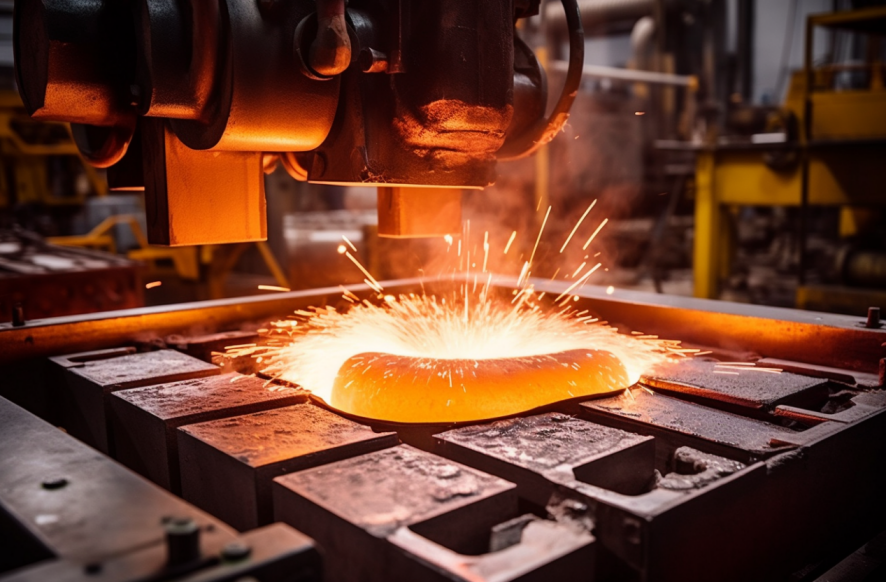
1. Understanding the Metal Forging Process
1.1 Definition and Overview
What is Custom Metal Forging?
Custom metal forging is a manufacturing technique involving the shaping of metal using localized compressive forces. Unlike casting, forging enhances the metal’s mechanical properties due to the aligned grain structure created during the process. This results in products with superior strength, durability, and resilience.
1.2 Types of Forging
Open-Die Forging
Open-die forging, also known as smith forging, involves deforming a piece of metal between multiple dies that do not enclose the metal entirely. This type of forging is suitable for large components and allows for more flexibility in shape and size.
Closed-Die Forging
Closed-die forging, or impression-die forging, involves pressing the metal into a die that contains a pre-cut shape. This method is ideal for producing high-precision components with complex shapes and is commonly used in the automotive and aerospace industries.
Rolled Ring Forging
Rolled ring forging starts with a circular metal piece which is then pierced to create a hollow ring. This ring is heated and rolled, increasing its diameter and reducing its thickness. The result is a strong, seamless ring used in various applications, including bearings, gears, and flanges.
1.3 Materials Used
Common Metals
Several metals are commonly used in forging due to their strength and durability. These include:
Steel: Known for its strength and versatility.
Aluminum: Valued for its lightweight properties and resistance to corrosion.
Titanium: Notable for its high strength-to-weight ratio and corrosion resistance.
Alloys
Alloys combine two or more elements to enhance the metal’s properties. Examples include:
Stainless Steel: Resists rust and corrosion, making it ideal for harsh environments.
Brass: An alloy of copper and zinc, known for its corrosion resistance and aesthetic appeal.
1.4 Steps in the Forging Process
Heating
The metal is heated to a specific temperature to make it malleable without melting it. This step is crucial for achieving the desired shape and mechanical properties.
Shaping
The heated metal is then placed between dies and subjected to compressive forces to shape it. This can be done through hammering, pressing, or rolling, depending on the type of forging.
Cooling
Once the desired shape is achieved, the metal is cooled to solidify its structure. Controlled cooling can enhance certain properties, such as hardness and strength.
1.5 Advantages
Strength
Forged parts are inherently stronger than those made through other manufacturing processes due to the alignment of the metal’s grain structure.
Durability
The compressive forces used in forging improve the metal’s structural integrity, making forged components more durable and capable of withstanding heavy loads and impacts.
Versatility
Custom metal forging offers flexibility in terms of design and material choices, allowing for the production of a wide range of components tailored to specific needs.
2. Benefits of Custom Metal Forging for Various Industries
2.1 Automobile Accessory Parts
Enhanced Performance
Custom metal forging produces high-strength components, such as suspension parts, that improve vehicle performance and safety. These parts can withstand significant stress and impact, ensuring longevity and reliability.
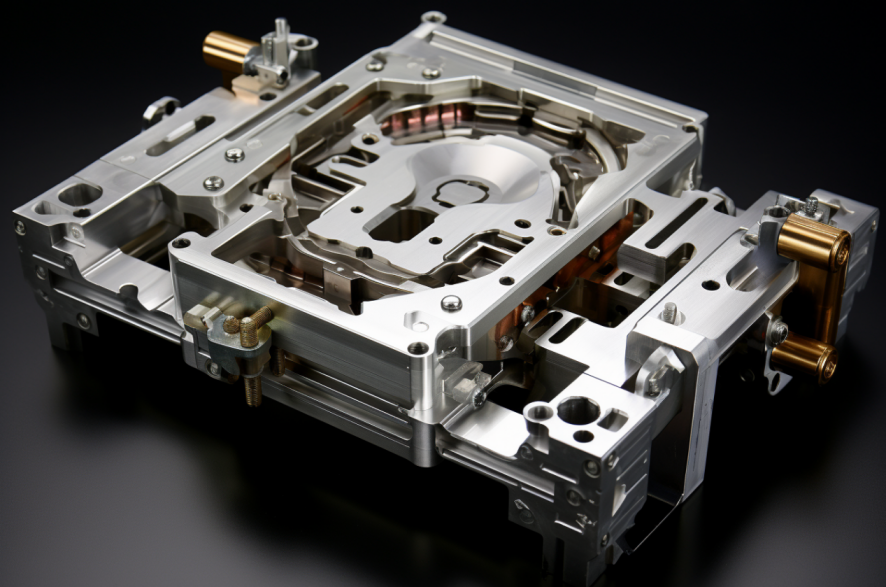
Weight Reduction
Forged aluminum parts are lighter than their cast counterparts, contributing to overall vehicle weight reduction and improved fuel efficiency. This is crucial for modern automotive design, where efficiency and performance are paramount.
Precision
The precision achieved through closed-die forging ensures that each component fits perfectly within the larger assembly, reducing the need for further machining and minimizing production costs.
2.2 Electronic Consumer Products
Durability
Forged components in electronic devices, such as connectors and enclosures, offer superior durability and longevity. This is particularly important for portable electronics that are subjected to frequent handling and potential impacts.
Heat Resistance
Forging enhances the thermal properties of metals, making them suitable for electronic components that must withstand high temperatures without degrading.
Aesthetic Appeal
Forged metal parts can be designed with intricate shapes and smooth finishes, enhancing the aesthetic appeal of consumer electronics while maintaining functional integrity.
2.3 Precision Hardware Parts
High Tolerance
Forging processes can achieve high tolerances, essential for precision hardware parts used in machinery and equipment where exact measurements are critical for performance.
Reliability
Forged hardware parts, such as bolts, nuts, and gears, exhibit exceptional reliability and strength, making them ideal for heavy-duty applications in various industries.
Customization
Custom forging allows for the production of specialized hardware parts tailored to specific applications, ensuring optimal performance and compatibility.
3. Choosing the Right Forging Service
3.1 Factors to Consider
Experience
When selecting a forging service provider like Louis Machine, it’s essential to consider their experience in the industry. A company with a proven track record can offer valuable insights and expertise, ensuring high-quality results.
Capabilities
Assess the capabilities of the forging service, including the types of forging they specialize in and the range of materials they can work with. Ensure they have the equipment and technology to meet your specific needs.
Certifications
Look for certifications such as ISO 9001, which indicate a commitment to quality management and continuous improvement. These certifications ensure that the forging service adheres to industry standards and best practices.
3.2 Customization Options
Tailored Solutions
Choose a forging service that offers customization options to tailor the process to your specific requirements. This includes the ability to produce components with unique shapes, sizes, and material properties.
Design Assistance
A good forging service provider will offer design assistance to help you optimize your component designs for the forging process, ensuring the best possible outcomes.
Prototyping
Consider whether the forging service can provide prototyping services to test and refine your designs before full-scale production, minimizing the risk of errors and ensuring quality.
3.3 Quality Control
Precision
Ensure the forging service employs rigorous quality control measures to guarantee precision and adherence to specifications. This includes regular inspections and testing throughout the forging process.
Standards Compliance
Verify that the forging service complies with relevant industry standards and regulations, ensuring the safety and reliability of the forged components.
Continuous Improvement
A commitment to continuous improvement is crucial for maintaining high standards of quality. Look for forging services that regularly update their processes and technologies to enhance their capabilities.
3.4 Technological Advancements
Modern Techniques
Choose a forging service that incorporates modern techniques and equipment, such as computer-aided design (CAD) and automation, to improve efficiency and precision.
Innovative Equipment
Ensure the forging service uses state-of-the-art equipment, such as induction heating systems and advanced forging presses, to achieve the best results.
Research and Development
A forging service with a strong focus on research and development can offer innovative solutions and stay ahead of industry trends, providing you with cutting-edge components.
3.5 Customer Support
Communication
Effective communication is vital for a successful forging project. Choose a forging service that prioritizes clear and open communication, keeping you informed at every stage of the process.
Collaboration
A collaborative approach ensures that the forging service understands your needs and works closely with you to achieve your goals. This includes regular consultations and feedback sessions.
Post-Sale Support
Consider the level of post-sale support offered by the forging service. This includes assistance with any issues that may arise after delivery and ongoing maintenance and support services.
Conclusion
Custom metal forging is an essential manufacturing process that offers unmatched strength, durability, and versatility for a wide range of industries. From automobile accessory parts to precision hardware components, the benefits of forging are evident in the enhanced performance, reliability, and customization options it provides.
When choosing a custom metal forging service provider like Louis Machine, consider factors such as experience, capabilities, and certifications. Ensure they offer tailored solutions, rigorous quality control, and incorporate modern technological advancements. Effective communication and collaboration are also crucial for a successful forging project.
By understanding the metal forging process and its benefits, you can make informed decisions and leverage the expertise of a reputable forging service provider to achieve high-quality, customized components that meet your specific needs.