Blog
We regularly update articles related to the prototyping and manufacturing industry. You’re welcome to check our previous blogs and subscribe to our newsletter.
How Does Cold Forming Ensure High-Quality Surface Finishes?
Explore the world of cold forming, a precision manufacturing process used across automotive, and electronics industries. Learn about its benefits, applications, and the challenges in precision mold design, plastic injection molding, and metal hardware parts production. Discover how Louis Machine, a leading cold forming service supplier, leverages advanced technology and customized solutions to deliver high-quality components. Dive into the intricacies of this efficient process and its role in producing durable, precise parts that meet the stringent requirements of modern manufacturing.
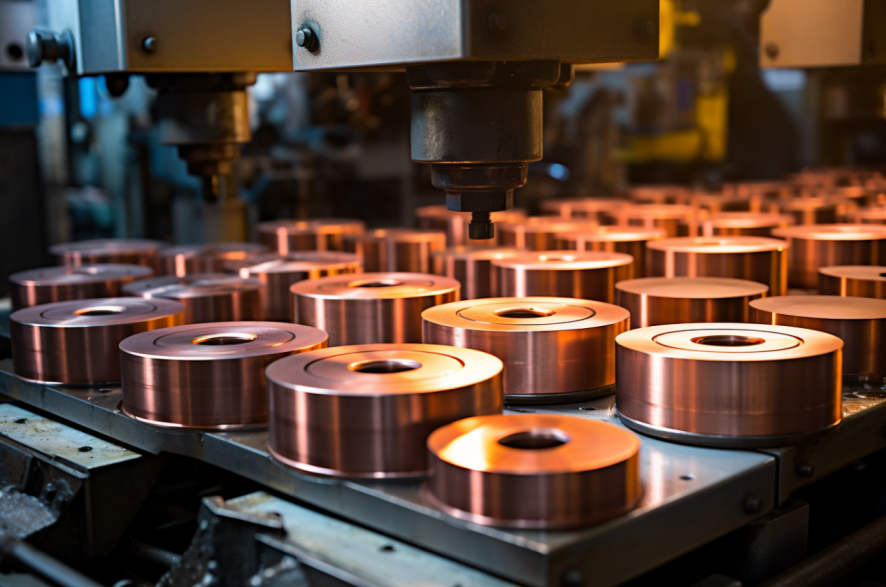
What is Cold Forming?
1.1 Definition and Process
Cold forming, also known as cold forging, is a manufacturing process in which metal is shaped at or near room temperature. Unlike hot forming, which involves heating metals to high temperatures, cold forming relies on high pressure to deform the material. This method is especially efficient for producing components with excellent mechanical properties, as the process enhances the metal’s strength through work hardening.
1.2 Benefits of Cold Forming
The cold forming process offers several benefits over traditional metal forming techniques. One of the primary advantages is the improved strength and durability of the final product. The cold working of the material increases its yield strength and hardness. Additionally, cold forming is highly efficient, leading to lower material waste and reduced production costs. The process also provides excellent surface finish and dimensional accuracy, minimizing the need for secondary machining operations.
1.3 Materials Used in Cold Forming
Cold forming is applicable to a variety of metals, including aluminum, brass, copper, stainless steel, and certain alloys. The choice of material depends on the desired properties of the finished product and the specific application requirements. Each metal behaves differently under cold forming conditions, necessitating careful consideration during the design and planning stages.
Applications of Cold Forming
2.1 Automotive Industry
Cold forming is extensively used in the automotive industry to manufacture a wide range of components.
Engine and Transmission Components
Engine and transmission parts, such as gears, shafts, and fasteners, benefit from the strength and precision provided by cold forming. These components are critical to the performance and reliability of vehicles, making cold forming an ideal production method.
Structural Parts
Cold forming is also employed to produce various structural parts for automobiles, including brackets, supports, and reinforcements. The high strength and accuracy of cold-formed parts ensure the safety and stability of the vehicle’s structure.
Electrical and Electronic Connectors
In addition, cold forming is used to produce electrical and electronic connectors, which require precise dimensions and excellent conductivity. The process ensures that these components meet the stringent quality standards of the automotive industry.
2.2 Aerospace Industry
The aerospace industry demands components that can withstand extreme conditions and stresses. Cold forming plays a crucial role in meeting these requirements.
Aircraft Fasteners
Aircraft fasteners, such as bolts and rivets, are commonly produced using cold forming. These fasteners must possess high strength and reliability to ensure the safety of the aircraft.
Structural Components
Structural components in aerospace applications, including brackets and supports, also benefit from the precision and strength provided by cold forming. The process ensures that these parts meet the stringent tolerances required in aerospace engineering.
Engine Components
Cold forming is used to manufacture various engine components for aerospace applications. The high strength and durability of cold-formed parts contribute to the overall performance and efficiency of aircraft engines.
2.3 Electronics Industry
In the electronics industry, cold forming is used to produce a variety of small, intricate components.
Connectors and Terminals
Connectors and terminals, essential for electrical connections in electronic devices, are often manufactured using cold forming. The process ensures precise dimensions and reliable performance.
Heat Sinks
Heat sinks, used for thermal management in electronic devices, are also produced through cold forming. The high precision of the process ensures efficient heat dissipation, enhancing the performance and longevity of electronic components.
Shielding Components
Cold forming is employed to produce shielding components that protect electronic devices from electromagnetic interference. The process ensures that these components meet the stringent requirements for effective shielding.
Industries Needs and Challenges
3.1 Precision Mold Design and Manufacturing
High Tolerance Requirements
One of the primary challenges in precision mold design is meeting the high tolerance requirements of modern manufacturing. Precision molds must be designed to produce parts with exact dimensions and minimal deviations, necessitating advanced design and manufacturing techniques.
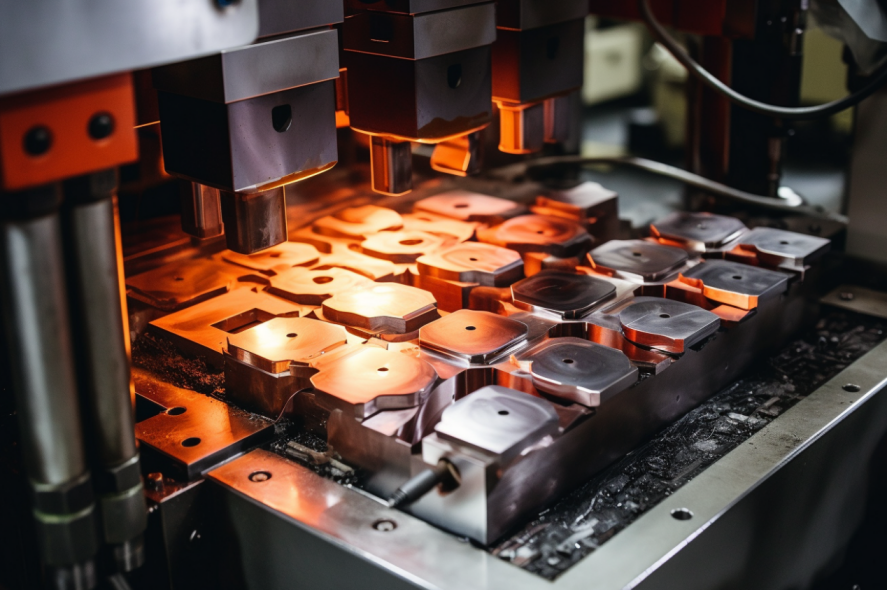
Material Selection
Selecting the right material for precision molds is crucial. The material must withstand the stresses of the cold forming process while maintaining its integrity and performance over repeated use. This requires careful consideration of material properties and compatibility with the forming process.
Cost Efficiency
Cost efficiency is another significant challenge in precision mold design and manufacturing. Developing and producing precision molds can be expensive, and manufacturers must balance the need for high-quality molds with cost constraints. Advanced technologies and innovative design approaches can help address this challenge.
3.2 Plastic Injection Molding Production
Complex Geometry
Producing parts with complex geometry using plastic injection molding is challenging. The molds must be designed to accommodate intricate shapes and fine details, requiring advanced engineering and manufacturing techniques.
Material Flow
Ensuring proper material flow during the injection molding process is critical to producing high-quality parts. Inadequate material flow can result in defects such as voids, warping, and incomplete filling, necessitating careful design and process control.
Cycle Time Reduction
Reducing cycle time is essential for improving production efficiency in plastic injection molding. Manufacturers must optimize the molding process to minimize cycle time while maintaining part quality, which involves fine-tuning various parameters and employing advanced technologies.
3.3 Metal Hardware Parts Processing Production
Precision Machining
Precision machining is essential for producing metal hardware parts with tight tolerances and high-quality finishes. This requires advanced machining equipment and techniques, as well as skilled operators who can ensure the accuracy and consistency of the machining process.
Surface Finish
Achieving the desired surface finish on metal hardware parts is a significant challenge. The surface finish affects the performance, appearance, and durability of the parts, necessitating careful selection of machining parameters and post-processing techniques.
Material Handling
Proper material handling is crucial in metal hardware parts processing. This includes managing the storage, transportation, and processing of raw materials to ensure their quality and integrity are maintained throughout the production process.
3.4 Automotive Parts Manufacturing
High Strength Requirements
Automotive parts must meet high strength requirements to ensure the safety and reliability of vehicles. This necessitates the use of advanced materials and manufacturing processes that can produce parts with the required strength and durability.
Lightweight Design
Reducing the weight of automotive parts is essential for improving fuel efficiency and performance. Manufacturers must balance the need for lightweight designs with the requirement for strength and safety, employing innovative materials and design approaches.
Regulatory Compliance
Automotive parts manufacturing is subject to stringent regulatory requirements. Manufacturers must ensure that their parts comply with industry standards and regulations, which can vary by region and application. This involves rigorous testing and quality control measures.
Cold Forming Service Supplier: Louis Machine
4.1 Expertise and Experience
Louis Machine is a leading supplier of cold forming services, with extensive expertise and experience in the industry. The company has a proven track record of delivering high-quality cold-formed parts to a wide range of industries, including automotive, aerospace, and electronics.
4.2 Advanced Technology
Louis Machine employs advanced technology and equipment to ensure the precision and quality of their cold-formed parts. The company’s state-of-the-art facilities enable them to produce complex components with tight tolerances and excellent surface finishes.
4.3 Customized Solutions
Louis Machine offers customized solutions to meet the specific needs of their clients. The company’s team of experts works closely with customers to develop tailored cold forming processes that address their unique requirements, ensuring optimal performance and cost-efficiency.
4.4 Commitment to Quality
Quality is a top priority for Louis Machine. The company adheres to stringent quality control measures throughout the manufacturing process, ensuring that every part meets the highest standards of performance and reliability. Louis Machine’s commitment to quality has earned them a reputation as a trusted partner in the cold forming industry.
Conclusion
In conclusion, cold forming is a versatile and efficient manufacturing process with applications across various industries. Despite the challenges faced in precision mold design, plastic injection molding, metal hardware processing, and automotive parts manufacturing, advancements in technology and innovative approaches continue to drive the industry forward. Companies like Louis Machine play a crucial role in delivering high-quality cold-formed parts, and meeting the evolving needs of their customers.