Blog
We regularly update articles related to the prototyping and manufacturing industry. You’re welcome to check our previous blogs and subscribe to our newsletter.
How Does the MIM Process Transform Design Ideas into High-Quality Metal Components?
Metal Injection Molding (MIM) stands as a pinnacle in modern manufacturing, revolutionizing the production of intricate metal components. At the helm of this transformative MIM process stands Louis Machine, a renowned manufacturer dedicated to pushing the boundaries of precision engineering. Let’s delve into the multifaceted world of MIM through the lens of Louis Machine’s exemplary work.
Market Trends: A Glimpse into the Future
1.1 Rising Demand for Complex Components
In today’s competitive landscape, manufacturers are constantly seeking ways to differentiate themselves. This has led to a surge in demand for complex components that can only be achieved through advanced manufacturing techniques like MIM. Louis Machine recognizes this trend and is well-positioned to cater to the growing demand for intricate and precise metal parts.
1.2 Focus on Cost-Effective Solutions
Cost-effectiveness remains a key driving factor in the market for MIM process solutions. Manufacturers are under pressure to optimize production costs without compromising on quality. Louis Machine’s expertise in custom MIM process solutions allows them to develop cost-effective manufacturing processes tailored to the specific needs of their clients, ensuring maximum value for every dollar spent.
1.3 Shift towards Sustainable Manufacturing
Sustainability has emerged as a top priority for businesses across industries. MIM process offers a sustainable alternative to traditional manufacturing methods by minimizing material waste and energy consumption. Louis Machine is committed to sustainable practices and offers eco-friendly MIM solutions that align with the growing emphasis on environmental responsibility.
Custom Solutions: The Key to Success
2.1 Understanding the Importance of Customization
In today’s dynamic market landscape, one size does not fit all. Each industry, each application has its own unique requirements when it comes to metal components. Louis Machine understands the importance of customization and works closely with clients to develop bespoke MIM solutions tailored to their specific needs.
2.2 Collaborative Approach to Problem-Solving
Louis Machine adopts a collaborative approach to problem-solving, partnering with clients every step of the way to ensure that their custom MIM solutions meet and exceed expectations. By leveraging their expertise in materials science, engineering, and manufacturing, Louis Machine delivers innovative solutions that address even the most complex challenges.
2.3 Flexibility in Design and Production
Flexibility is a hallmark of Louis Machine’s approach to custom MIM solutions. Whether it’s a small batch of highly specialized components or a large-scale production run, Louis Machine has the capability to adapt to the unique requirements of each project. From design optimization to post-processing, every aspect of the production process is tailored to achieve the desired outcome.
Game Console Handle Mold: Crafting Excellence through Innovation
3.1 Grinding, CNC Milling, Wire-Electrode Cutting, and Discharge Processing EDM: The Art of Fusion
In the creation of the Game Console Handle Mold, Louis Machine employs a symphony of techniques. Grinding ensures the fine-tuning of surfaces, while CNC milling carves out precise dimensions with unparalleled accuracy. Wire-electrode cutting adds a layer of intricacy, allowing for the formation of complex geometries. Finally, Discharge Processing EDM emerges as the star player, boasting an impressive accuracy of +/-0.003mm. This amalgamation of methods underscores Louis Machine’s commitment to delivering excellence through innovation.
3.2 Embracing Complexity: The Journey to Perfection
With each component of the Game Console Handle Mold, Louis Machine embraces complexity with open arms. The 56 die hole cavities, meticulously crafted with Discharge Processing EDM, exemplify the pursuit of perfection. Uniform roughness and stringent control over cavity depth size error further showcase Louis Machine’s unwavering dedication to precision engineering.
Discharge Processing EDM: Setting the Standard for Precision
4.1 Precision Redefined: The Power of Discharge Processing EDM
Louis Machine’s Discharge Processing EDM sets the gold standard for precision manufacturing. Boasting an astonishing accuracy of +/-0.003mm, this process leaves no room for error. The 56 die hole cavities, each flawlessly executed, speak volumes about Louis Machine’s mastery over the craft. Moreover, the emphasis on uniform roughness ensures a seamless finish, elevating the final product to new heights of excellence.
4.2 Tightening the Reins: Controlling Cavity Depth Size Error
In the realm of precision engineering, control is paramount. Louis Machine understands this implicitly, exemplified by their meticulous control over cavity depth size error. With a precision of +/-0.003mm, every aspect of the Discharge Processing EDM is scrutinized to perfection. This unwavering attention to detail ensures that each component meets the highest standards of quality and accuracy.
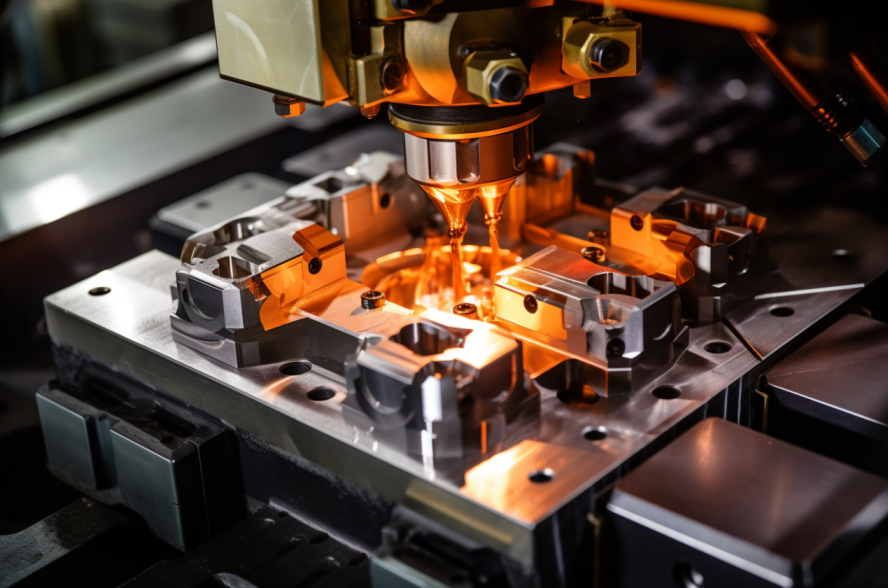
Precision Carrier Plates: Pioneering Efficiency in Production
5.1 Versatility Personified: The Role of Precision Carrier Plates
Louis Machine’s Precision Carrier Plates epitomize versatility in manufacturing. Crafted from an array of raw materials such as stainless steel and powder stainless steel, these plates are the cornerstone of mass rapid conversion production. From mobile phone metal frames to circuit board components assembly, Louis Machine’s Precision Carrier Plates pave the way for efficiency and innovation.
5.2 Driving Innovation: The Promise of Mass Rapid Conversion Production
In today’s fast-paced world, efficiency is key. Louis Machine’s Precision Carrier Plates deliver on this promise, enabling mass rapid conversion production with unparalleled ease. By leveraging a diverse range of raw materials, Louis Machine empowers industries to push the boundaries of innovation. Whether it’s the sleek contours of a mobile phone frame or the intricate assembly of circuit board components, Louis Machine’s Precision Carrier Plates stand as a testament to the endless possibilities of modern manufacturing.
A Symphony of Machines: The Essence of Mass Production
6.1 Embracing Technology: The Role of CNC Lathes
At Louis Machine, the mass production of metal parts is a symphony of machines in motion. CNC lathes take center stage, meticulously crafting components with unparalleled precision. The integration of Automatic CNC lathes further streamlines the production process, ensuring seamless efficiency at every turn. Together, these machines form the backbone of Louis Machine’s commitment to excellence in manufacturing.
6.2 Materials Matter: Stainless Steel, Copper, Aluminum
In the pursuit of perfection, Louis Machine leaves no stone unturned. Working with an array of materials including stainless steel, copper, and aluminum, Louis Machine ensures versatility without compromise. Each material presents its own set of challenges, yet Louis Machine rises to the occasion, delivering metal parts with delicate surface texture and size accuracy of +/-0.003mm.
Mastering Complexity: The Art of 3D Curved Surface Machining
7.1 Pushing Boundaries: CNC Milling Machines
Complex 3D curved surface machining heralds a new era of possibility for Louis Machine. With the aid of CNC milling machines, Louis Machine ventures into uncharted territory, pushing the boundaries of what’s possible. Intricate designs come to life as these machines carve out precise contours with surgical precision.
7.2 Precision Redefined: Surface Texture and Hardness
In the realm of 3D curved surface machining, precision reigns supreme. Louis Machine understands this implicitly, demanding nothing short of perfection. From achieving very fine surface texture to ensuring optimal hardness, Louis Machine leaves no stone unturned. With a combined machining accuracy of +/-0.002mm, Louis Machine sets the gold standard for precision engineering.
Varo Precision Mold Parts: Elevating Excellence through Precision
8.1 The Precision Paragon: Discharge Processing EDM
Varo Precision Mold Parts epitomize excellence in precision engineering. With a laser focus on accuracy, Louis Machine leverages Discharge Processing EDM to achieve remarkable results. With an accuracy of +/-0.003mm, Louis Machine ensures that every component meets the highest standards of quality.
8.2 Uniformity Unleashed: Grinding Processing
In the pursuit of perfection, uniformity is paramount. Louis Machine understands this implicitly, exemplified by their emphasis on extremely uniform harshness. Through grinding processing with an accuracy of +/-0.002mm, Louis Machine ensures that each component is flawless, inside and out.
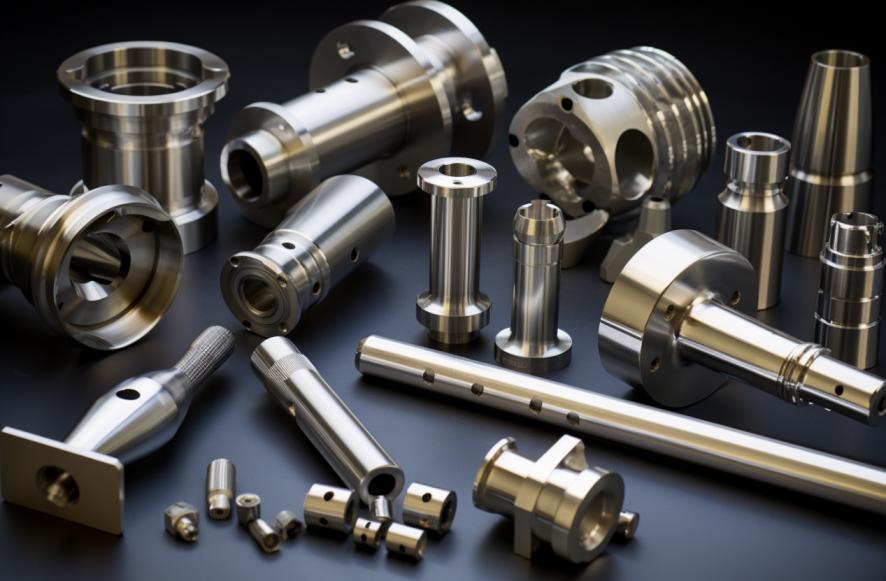
Conclusion: A Glimpse into the Future of Manufacturing
As we journey through the intricate world of MIM process, one thing becomes abundantly clear: Louis Machine is at the forefront of innovation. Through their mastery of grinding, CNC milling, wire-electrode cutting, and Discharge Processing EDM, Louis Machine continues to redefine the boundaries of precision engineering. With their unwavering commitment to excellence, Louis Machine is not just shaping the future of manufacturing – they are paving the way for a new era of possibility.