Blog
We regularly update articles related to the prototyping and manufacturing industry. You’re welcome to check our previous blogs and subscribe to our newsletter.
How Are Mold and Hardware Manufacturers Embracing Eco-Friendly Practices?
In the realm of hardware manufacturing, molds play a pivotal role in shaping precision parts that form the backbone of various industries. At the heart of this intricate process lies a symbiotic relationship between mold and hardware manufacturers. Let’s delve deeper into how Louis Machine, a leading player in this field, orchestrates this synergy to deliver exceptional results.
Understanding Molds in Hardware Manufacturing:
1.1 Definition and Function of Molds:
Molds are intricate tools used in the hardware manufacturing process to shape raw materials into precise components. These molds come in various forms, from simple to highly complex designs, depending on the intricacy of the hardware being produced. At Louis Machine, each mold is crafted with meticulous attention to detail to ensure flawless execution.
1.2 Importance of Precision and Quality:
Precision and quality are non-negotiable aspects of mold design and fabrication. A minor deviation can lead to significant repercussions in the final product’s performance and integrity. Louis Machine upholds uncompromising standards in both precision and quality, leveraging cutting-edge technologies and skilled craftsmanship to deliver molds that exceed industry expectations.
Market Status: Trends and Challenges
The mold and hardware manufacturing market is witnessing steady growth, driven by diverse industries seeking customized solutions and advanced technologies. However, several challenges persist, impacting the efficiency and competitiveness of manufacturers.
2.1 Rising Demand for Precision
In industries like automotive and aerospace, the need for precision components is paramount. Manufacturers must deliver molds and hardware that meet tight tolerances and stringent quality standards. Achieving such precision requires advanced machining capabilities and meticulous quality control measures.
2.2 Pressure for Cost Efficiency
Cost considerations remain a key factor for both manufacturers and their clients. With increasing competition and fluctuating raw material prices, achieving cost efficiency without compromising quality is a constant challenge. Manufacturers must streamline processes, optimize resource utilization, and explore innovative cost-saving measures.
2.3 Adapting to Technological Advancements
Technological advancements, including automation, additive manufacturing, and digitalization, are reshaping the mold and hardware manufacturing landscape. Embracing these technologies is essential for staying competitive and meeting evolving customer demands. However, the integration of new technologies often requires significant investments and workforce upskilling.
Custom Mold Solutions for Mold and Hardware Manufacturers:
To address the dynamic market needs and overcome challenges, mold and hardware manufacturers like Louis Machine are implementing strategic initiatives and innovative solutions.
3.1 Investment in Advanced Machining Technologies
Louis Machine recognizes the importance of staying at the forefront of machining technologies. By investing in state-of-the-art CNC machining equipment, they enhance their capabilities to produce complex molds and precision hardware with utmost efficiency and accuracy.
3.2 Focus on Research and Development
Continuous innovation is central to Louis Machine’s strategy. They allocate significant resources to research and development, collaborating with industry experts and leveraging cutting-edge technologies to develop novel solutions. This proactive approach enables them to anticipate market trends and deliver innovative products that address evolving customer needs.
3.3 Embracing Sustainable Practices
Sustainability is gaining prominence across industries, prompting Mold and Hardware Manufacturers to adopt eco-friendly practices. Louis Machine prioritizes sustainability in its operations, employing recyclable materials, optimizing energy usage, and implementing waste reduction measures. By aligning with environmentally conscious principles, they not only contribute to a greener future but also appeal to environmentally aware customers.
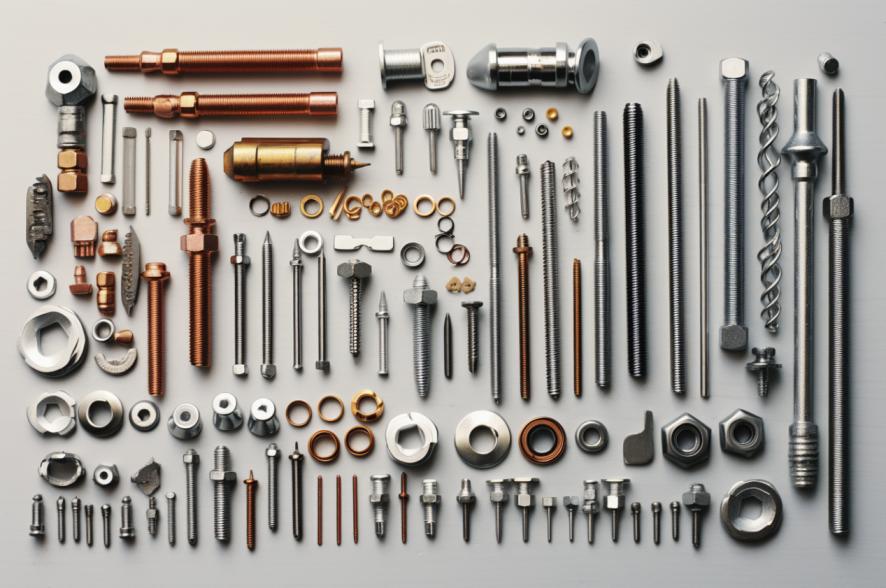
Precision Hardware Parts:
4.1 Game Console Handle Mold:
Louis Machine’s expertise extends to crafting molds for a myriad of hardware components, including game console handles. These molds undergo a rigorous manufacturing process, including grinding, CNC milling, wire-electrode cutting, and discharge processing EDM, to achieve unparalleled precision and durability.
4.2 Discharge Processing EDM:
With an accuracy reaching +/-0.003mm and meticulously controlled cavity depth sizes, Louis Machine sets the benchmark for excellence in discharge processing EDM. Whether it’s precision carrier plates or mass-produced metal parts, every detail is meticulously crafted to perfection.
4.3 Mass Production of Metal Parts:
Louis Machine’s capabilities extend beyond mold fabrication to mass production of metal parts using CNC lathe, automatic CNC lathe, turning, and milling composite machine tools. From stainless steel to copper and aluminum, each product boasts impeccable surface texture and size accuracy.
4.4 Innovations in CNC Milling:
Complex 3D curved surfaces pose no challenge for Louis Machine’s CNC milling machines. With stringent requirements for surface texture and hardness, combined with a machining accuracy of +/-0.002mm, Louis Machine delivers flawless results that redefine industry standards.
4.5 Varo Precision Mold Parts:
The Varo precision mold parts exemplify Louis Machine’s commitment to excellence. With discharge processing EDM accuracy of +/-0.003mm and uniformly distributed harshness, coupled with grinding processing accuracy of +/-0.002mm, these parts epitomize precision engineering at its finest.
Material Selection and Compatibility:
5.1 Choosing the Right Materials:
The foundation of any successful mold lies in selecting the appropriate materials tailored to the hardware being produced. Louis Machine meticulously evaluates factors such as durability, thermal conductivity, and chemical resistance to ensure optimal performance and longevity of the molds.
5.2 Compatibility Considerations:
Harmonizing mold materials with hardware materials is crucial to prevent compatibility issues that could compromise product quality. Louis Machine conducts rigorous compatibility tests to ascertain seamless integration between mold and hardware materials, mitigating risks and ensuring flawless production processes.
Efficiency and Cost-Effectiveness:
6.1 Optimizing Mold Design and Manufacturing Processes:
Louis Machine’s relentless pursuit of efficiency drives continuous improvement in mold design and manufacturing processes. By leveraging advanced technologies and innovative methodologies, Louis Machine streamlines workflows minimizes lead times, and maximizes output without compromising quality.
6.2 Cost-Saving Strategies:
Efficient mold production and maintenance are integral components of Louis Machine’s cost-saving strategies. Through proactive maintenance schedules, predictive analytics, and optimized production schedules, Louis Machine reduces downtime, lowers operational costs, and enhances overall profitability for its clients.
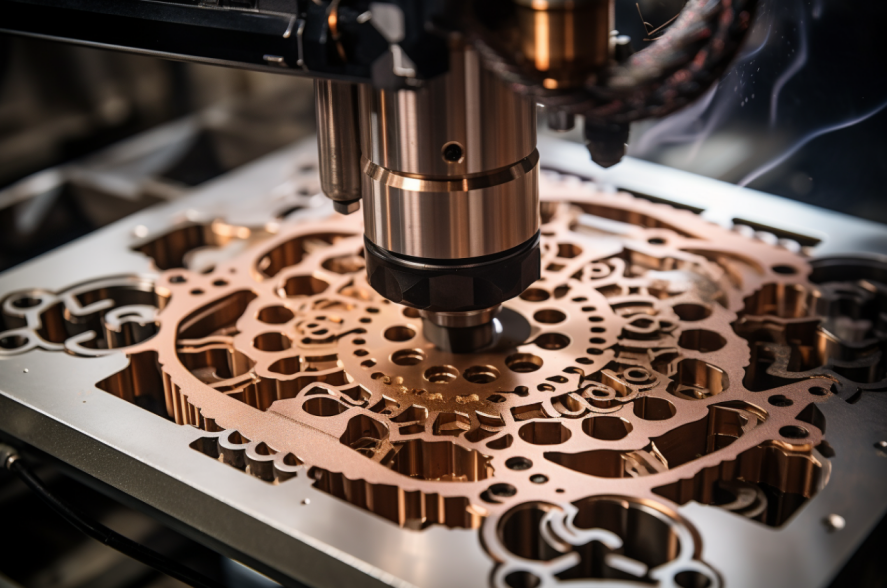
Innovations in Mold Technology:
7.1 Recent Advancements:
Louis Machine remains at the forefront of mold technology, constantly innovating to meet the evolving needs of hardware manufacturers. Recent advancements encompass a spectrum of innovations, from novel materials and coatings to state-of-the-art design software and additive manufacturing techniques.
7.2 Examples of Innovative Designs:
Louis Machine’s portfolio boasts a myriad of innovative mold designs and materials that revolutionize manufacturing processes. From intricate geometries and microstructures to lightweight and durable composites, these innovations optimize performance, increase product lifespan, and unlock new possibilities for hardware manufacturers.
Collaboration and Partnership:
8.1 Value of Collaboration:
Collaboration between mold and hardware manufacturers is more than a transactional relationship—it’s a symbiotic partnership that fosters mutual growth and success. Louis Machine recognizes the value of collaboration in sharing expertise, pooling resources, and co-creating innovative solutions that address industry challenges and drive competitiveness.
8.2 Successful Partnerships:
Louis Machine’s success stories are a testament to the power of collaboration and partnership. Through joint ventures, strategic alliances, and long-term relationships, Louis Machine has enabled hardware manufacturers to achieve breakthroughs in product development, cost optimization, and market expansion, cementing its position as a trusted partner in the industry.
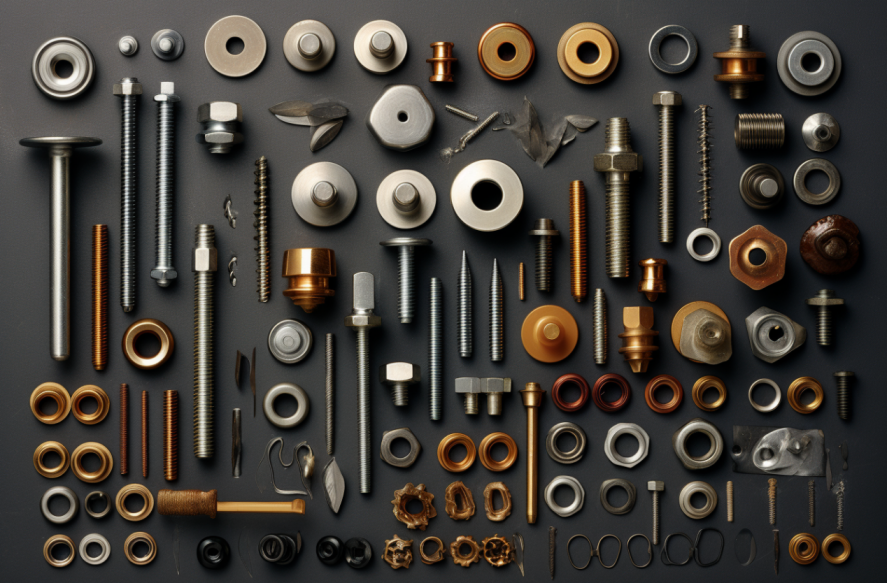
Conclusion:
Louis Machine stands as a beacon of innovation and excellence in the symbiotic realm of mold and hardware manufacturing. Through customized solutions, unwavering precision, and relentless pursuit of perfection, Louis Machine continues to elevate the standards of the industry, shaping the future of hardware manufacturing one precision part at a time.