Blog
We regularly update articles related to the prototyping and manufacturing industry. You’re welcome to check our previous blogs and subscribe to our newsletter.
Precision Engineering: How Multi Axis Machining Delivers Unrivaled Accuracy
In the current manufacturing scene, precision and efficiency are paramount. Multi-axis machining has emerged as a cornerstone technology, offering unparalleled versatility in crafting intricate components with absolute precision. Across varied sectors such as aerospace and medicine, multi-axis machining has revolutionized production, enabling the fabrication of complex geometries previously deemed unattainable.
Understanding Multi-Axis Machining
1. Evolution of Precision: Multi-axis machining represents a quantum leap in machining technology. It allows for simultaneous movement of the cutting tool along multiple axes, enabling intricate cuts and complex shapes with precision. Over the years, advancements in CNC technology and tooling have propelled multi-axis machining to new heights, facilitating the production of components that were previously unfeasible.
2. Applications Across Industries: The significance of multi-axis machining transcends industries. In aerospace, it facilitates the production of lightweight yet robust components for aircraft and spacecraft. In the medical field, it enables the creation of intricate implants and surgical instruments. Automotive manufacturers leverage multi-axis machining for engine components and vehicle body parts. Its applications are vast and diverse, catering to the needs of various sectors seeking precision and complexity in their products.
3. Complex Geometries: One of the key advantages of multi-axis machining is its ability to achieve complex geometries with ease. Whether it’s intricate contours, sharp angles, or sculpted surfaces, multi-axis machining excels in transforming digital designs into tangible components with utmost precision. This capability is invaluable in industries where form and function are paramount, such as aerospace and medical device manufacturing.
Types of Multi-Axis Machining
1. 3-Axis, 4-Axis, 5-Axis, and Beyond: Multi-axis machining encompasses a spectrum of configurations, each offering its own set of advantages and limitations. The traditional 3-axis setup allows for movement along the X, Y, and Z axes, suitable for relatively simple geometries. As we progress to 4-axis and 5-axis configurations, the machining capabilities expand, enabling access to complex features from multiple angles. Beyond 5-axis machining, such as 6-axis or more, further enhances the freedom of motion, opening doors to even more intricate designs.
2. Advantages and Limitations: Each configuration of multi-axis machining comes with its own set of advantages and limitations. While higher axis counts offer increased flexibility and accessibility, they also introduce challenges such as programming complexity and tool interference. Conversely, lower axis counts may be more straightforward to program and operate but may have limitations in machining certain geometries. Understanding these trade-offs is crucial in selecting the optimal machining strategy for a given application.
3. Louis Machine’s Expertise: As a leading multi-axis machining service provider, Louis Machine boasts a wealth of experience in leveraging various configurations to meet diverse customer needs. From precision aerospace components to intricate medical implants, Louis Machine delivers exceptional quality and reliability. With state-of-the-art equipment and a team of skilled machinists, Louis Machine stands at the forefront of multi-axis machining excellence.
Benefits of Multi-Axis Machining
1. Increased Productivity: Multi-axis machining offers significant gains in productivity compared to traditional machining methods. By reducing the need for multiple setups and tool changes, manufacturers can streamline their workflows and achieve faster turnaround times. This efficiency translates into cost savings and improved competitiveness in the market.
2. Improved Accuracy: Precision is the hallmark of multi-axis machining. By allowing simultaneous machining from multiple angles, it ensures superior dimensional accuracy and surface finish. Whether it’s tight tolerances or complex contours, multi-axis machining delivers consistent results with minimal deviation, ensuring the integrity of the final product.
3. Reduced Setup Times: Setup is a critical aspect of machining operations, often consuming valuable time and resources. It minimizes setup times by consolidating multiple operations into a single setup. This not only reduces downtime but also enhances workflow efficiency, allowing manufacturers to meet tight deadlines and customer demands.
4. Enhanced Surface Finish: Surface finish plays a crucial role in the performance and aesthetics of machined components. Multi-axis machining excels in achieving smooth surfaces and intricate textures, eliminating the need for secondary finishing operations. Whether it’s polishing, knurling, or engraving, multi-axis machining delivers pristine surfaces that meet the most stringent quality standards.
5. Real-World Examples: The impact of multi-axis machining can be seen across various industries. In aerospace, it enables the production of lightweight components with complex internal structures, improving fuel efficiency and performance. In the medical field, it facilitates the creation of patient-specific implants with intricate geometries, enhancing biocompatibility and functionality. From automotive to consumer electronics, it has become indispensable in realizing innovative designs and pushing the boundaries of what’s possible.
Driving Automotive Innovation
1. Pushing the Boundaries of Design
In the automotive sector, where innovation drives competitiveness, it offers automotive manufacturers the flexibility to push the boundaries of design and functionality. Whether crafting complex engine components or lightweight structural elements, multi-axis machining enables automotive engineers to optimize performance, reduce weight, and enhance fuel efficiency—all while maintaining stringent quality standards.

2. Example: Engine Cylinder Heads
Engine cylinder heads are critical components that demand both strength and precision. Multi-axis machining allows for the creation of intricate combustion chambers, precise valve seats, and optimized coolant passages, resulting in engines that deliver superior performance and fuel economy. Moreover, by consolidating multiple machining operations into a single setup, it streamlines production, reducing lead times and costs.
Revolutionizing Medical Manufacturing
1. Empowering Healthcare Innovation
In the medical field, where precision is a matter of life and death, it is revolutionizing the manufacturing of medical devices and implants. From intricate surgical instruments to patient-specific orthopedic implants, it enables medical manufacturers to produce customized solutions with unprecedented accuracy and speed, improving patient outcomes and quality of life.
2. Example: Orthopedic Implants
Orthopedic implants, such as hip and knee prostheses, must be tailored to each patient’s unique anatomy for optimal performance and longevity. It facilitates the fabrication of complex implant geometries with micron-level precision, ensuring proper fit and functionality. By leveraging advanced CAD/CAM software and multi-axis machining capabilities, medical manufacturers can deliver personalized implants that enhance patient mobility and comfort.
Empowering Tooling Innovation
1. Enabling Precision Manufacturing
In the realm of tooling and die making, where precision is paramount, multi-axis machining empowers manufacturers to produce high-quality molds, dies, and tooling inserts with unmatched precision and efficiency. Whether crafting intricate injection molds or complex stamping dies, multi-axis machining offers toolmakers the versatility and agility to meet the evolving demands of modern manufacturing.
2. Example: Injection Molds
Injection molding, a widely used manufacturing process, relies on precision molds to produce intricate plastic parts. It enables the creation of highly complex mold cavities with precise surface finishes and intricate geometries, ensuring the production of defect-free parts with tight tolerances. By optimizing mold design and machining processes, manufacturers can achieve faster cycle times, reduce scrap rates, and enhance overall productivity.
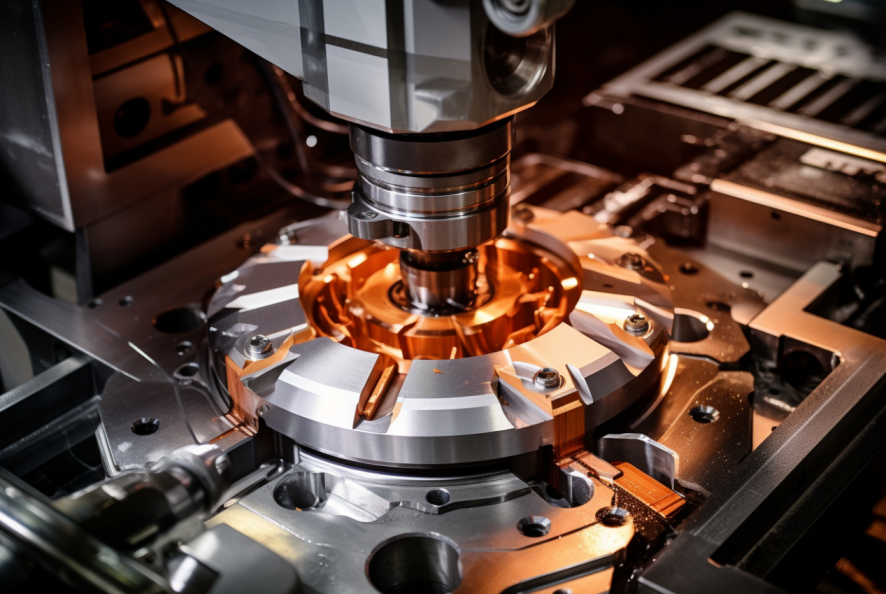
Conclusion
In conclusion, it represents a paradigm shift in modern manufacturing, unlocking new possibilities in precision, efficiency, and innovation. With its ability to achieve complex geometries with unparalleled accuracy, it has become the go-to technology for industries seeking to stay ahead of the curve. As exemplified by Louis Machine’s expertise and commitment to excellence, multi-axis machining continues to shape the future of manufacturing, driving progress and prosperity across industries.