Blog
We regularly update articles related to the prototyping and manufacturing industry. You’re welcome to check our previous blogs and subscribe to our newsletter.
Revolutionizing Prototyping with Plastic 3D Printing: Louis Machine’s Innovative Solutions
Before the advent of 3D printing, prototyping was a time-consuming and costly process, often involving manual craftsmanship and labor-intensive methods to create a single model. Mistakes or design changes meant starting over, leading to further delays and expenses.
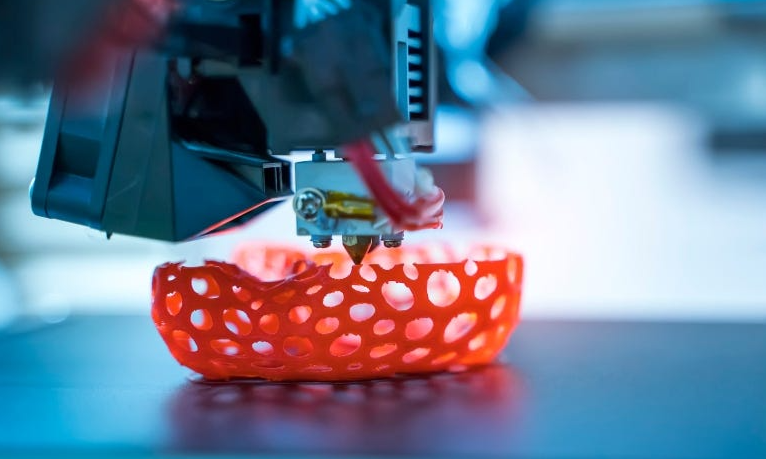
Louis Machine, a pioneering force in the Plastic 3D printing prototyping arena. Leveraging the transformative power of this technology, Louis Machine has significantly streamlined and innovated the prototyping process, introducing efficiency, precision, and flexibility previously unimaginable. Our influence in the sector has redefined the boundaries of design and manufacturing, marking a new era in product development.
Evolution of 3D Printing
Challenges Faced by Early 3D Printing Technologies in the 1980s
In the early days of 3D printing, which can be traced back to the 1980s, predominant techniques such as stereolithography and selective laser sintering had notable limitations. These methods were constrained by the types of materials they could employ, often relying on expensive and brittle resins or powders. Moreover, the machines were bulky and expensive, impeding their widespread adoption.
Transforming 3D Printing with Fused Deposition Modeling (FDM)
As 3D printing evolved, a significant shift occurred towards the preference for plastic as the primary material. Fused deposition modeling (FDM) technology, emerging in the 1990s, gained popularity for its utilization of thermoplastics like ABS and PLA. This transformation democratized 3D printing, making it more accessible and cost-effective. It enabled the creation of robust and functional prototypes and allowed for the customization of consumer products. Today, continuous advancements in materials science further broaden the horizons of 3D printing, facilitating the production of intricate structures, medical implants, and even edible items, all at reduced costs and with heightened versatility.
The Benefits of Plastic 3D Printing for Prototyping
Plastic 3D printing offers a plethora of advantages for prototyping, leading to a profound transformation in the product development process.
Enhanced Speed and Efficiency
Among its primary merits is the remarkable acceleration of prototyping processes. Traditional prototyping methods often entail prolonged timelines due to the necessity of crafting molds or toolings, a process that may span weeks or even months. Conversely, plastic 3D printing enables the rapid production of prototypes, slashing time-to-market for products. Furthermore, it facilitates seamless on-the-fly design modifications, supporting iterative development and swift adjustments in response to feedback.
Exceptional Cost Efficiency
Another compelling rationale for embracing plastic 3D printing lies in its cost-effectiveness. Unlike conventional approaches that frequently entail material wastage during mold or tool creation, 3D printing minimizes such waste. The absence of a requirement for costly moldings or toolings can translate into substantial cost savings, particularly beneficial for businesses engaged in small production runs or crafting one-of-a-kind prototypes.
Precision and Elaboration
Plastic 3D printing excels in the fabrication of prototypes characterized by intricate designs and meticulous details. Achieving such levels of precision can be challenging using traditional methods. This technology ensures consistently high-quality and replicable outcomes, rendering it ideally suited for crafting complex geometries, intricate patterns, and prototypes with finely nuanced features.
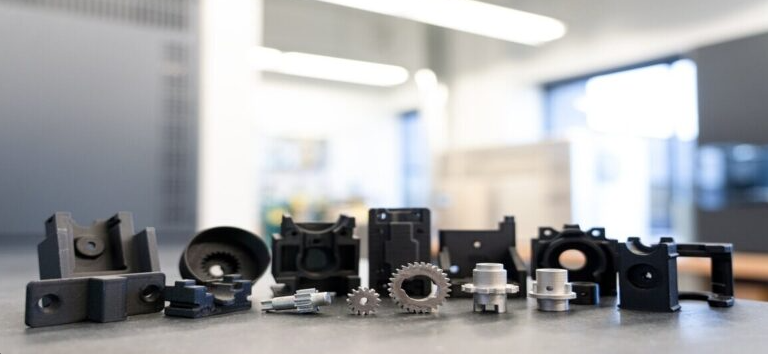
Commitment to Sustainability
The contemporary manufacturing landscape places an ever-greater emphasis on sustainability.Plastic 3D printing prototyping actively contributes to sustainability efforts on two fronts. Firstly, it permits the utilization of recyclable materials, thus minimizing the environmental footprint. Secondly, by reducing material waste and enabling the crafting of prototypes with lower energy consumption compared to traditional methods, it plays a pivotal role in diminishing the carbon footprint, aligning with environmentally friendly practices.
Louis Machine’s Innovative Solutions
Introducing Louis Machine’s Distinctive Approach
Louis Machine stands as a trailblazer in the realm of innovation, delivering exceptional solutions that redefine industrial processes. Our approach marries cutting-edge technology with an unwavering commitment to customization, empowering businesses to attain unprecedented levels of efficiency and excellence.
Leading-Edge Machinery and Technology
At the core of Louis Machine’s innovative prowess lies a comprehensive array of advanced machinery and technology. Our state-of-the-art equipment seamlessly integrates the latest advancements in automation, robotics, and artificial intelligence. This synergy yields manufacturing processes that are exceptionally efficient and precise, mitigating human errors and elevating overall productivity.
Tailored Solutions for Diverse Industries
What sets Louis Machine apart is our unparalleled ability to fashion solutions tailored to the unique demands of diverse industries. Be it automotive, aerospace, healthcare, or any other sector, we adeptly customize our technology to meet specific requirements. Our adaptable approach ensures that clients can optimize their operations, enhance product quality, and curtail costs, all while maintaining a competitive edge in their respective markets.
Showcasing Remarkable Success Stories
Louis Machine’s track record boasts a series of remarkable successes across a spectrum of industries. For instance, our CNC milling machine enables the precise machining of complex 3D curved surfaces, with stringent accuracy requirements of ±0.002mm. In the case of Varo precision mold parts, our EDM (Electrical Discharge Machining) achieves accuracy levels of ±0.003mm and uniform surface finish, while grinding processes maintain an accuracy of ±0.002mm. These case studies vividly illustrate our unwavering commitment to precision and excellence.
Challenges & Future Prospects
Present Challenges in Plastic 3D Printing
Despite its numerous advantages, plastic 3D printing confronts challenges, including limited material choices, speed constraints, and post-processing demands. Balancing high-speed production with quality preservation remains an ongoing challenge, while the material options can be constraining for specific applications.
Louis Machine’s Strategies for Overcoming These Hurdles
Louis Machine is actively addressing these challenges through continuous research and development efforts. They are engaged in the exploration of novel materials and the refinement of their printing processes to enhance both speed and precision. Moreover, Louis Machine is committed to the implementation of post-processing automation, streamlining the finishing stages and thereby reducing production time and costs.
Projections for the Future of 3D Printing and Prototyping
The future of 3D printing and prototyping holds great promise. Anticipated advancements encompass a broader array of materials, heightened printing speeds, and increased automation. Industries such as aerospace, healthcare, and automotive, where customization and rapid prototyping are essential, will see 3D printing play a pivotal role. As technology advances, 3D printing will persist in reshaping manufacturing processes, ushering in more sustainable and efficient production methods.
CONCLUSION
Louis Machine’s groundbreaking approach to Plastic 3D printing prototyping has transformed the prototyping field. Their dedication to state-of-the-art technology, tailor-made solutions, and an unwavering pursuit of perfection has yielded transformative outcomes. With the future holding the prospect of further breakthroughs in 3D printing and prototyping, Louis Machine is primed to remain at the forefront, consistently driving innovation and revolutionizing the realm of manufacturing.