Blog
We regularly update articles related to the prototyping and manufacturing industry. You’re welcome to check our previous blogs and subscribe to our newsletter.
Ensuring Precision: Sheet Metal Parts Proofing
In the world of manufacturing, sheet metal fabrication is a fundamental process with widespread applications. From automotive components to aerospace structures and household appliances, sheet metal parts play an essential role in numerous industries. However, achieving precision and quality in sheet metal fabrication is paramount, as even the slightest deviation can lead to costly defects and performance issues. This is where the concept of proofing sheet metal parts becomes crucial. Proofing involves a meticulous validation process that ensures the accuracy, fit, and functionality of sheet metal components before mass production. It not only helps identify potential issues but also contributes to cost savings and product reliability.
Understanding the Proofing Process
Role and Purpose of Proofing in Sheet Metal Fabrication
Proofing within the context of sheet metal fabrication encompasses a comprehensive validation and testing protocol applied to sheet metal components before mass production commences. Its fundamental objective is to ascertain that the designed parts conform precisely to specified dimensions, tolerances, and performance criteria. Positioned as a pivotal juncture in the production cycle, proofing is instrumental in identifying potential design flaws, material-related concerns, or manufacturing intricacies that might otherwise compromise the ultimate quality and functionality of the end product.
Crucial Role of Accuracy and Precision
At the core of sheet metal part proofing reside two pivotal attributes: accuracy and precision. Accuracy ensures the seamless alignment of component dimensions and features with the intended design, leaving no room for discrepancies. Precision, on the other hand, bestows upon the process a hallmark of uniformity and reproducibility in fabrication. Attaining the dual virtues of accuracy and precision assumes paramount importance, particularly in cases where sheet metal parts serve as integral constituents within intricate assemblies. Even the slightest deviations from these standards can precipitate issues related to fit, performance, or safety, underscoring the non-negotiable significance of these attributes in the proofing phase.
Common Challenges and Pitfalls in Sheet Metal Production
Sheet metal fabrication poses a unique set of challenges and potential pitfalls, reinforcing the indispensable nature of the proofing process. These challenges encompass a spectrum that includes meticulous material selection, meticulous management of tolerance stack-ups, intricate complexities tied to bending and forming, rigorous scrutiny of welding quality, and the meticulous handling of surface finish considerations. Proofing emerges as a potent tool for manufacturers, affording them the means to preemptively address and rectify these challenges in their nascent stages. This proactive approach not only averts the specter of costly rework but also forestalls production delays, thereby augmenting the overall quality and dependability of the sheet metal components.
Methods for Ensuring Precision in Sheet Metal Parts
Validation and Precision Modeling with CAD
Computer-Aided Design (CAD) Software: CAD software is foundational for verifying designs. Engineers employ it to craft detailed 2D and 3D models of sheet metal components, assuring adherence to precise specifications. CAD facilitates visualizing the end product and assists in early-stage detection of potential design flaws.
Finite Element Analysis (FEA): FEA, a potent computational tool, employs mathematical models to simulate how sheet metal parts will respond to various conditions. It aids in forecasting stress, deformation, and structural integrity. Engineers optimize designs for strength and performance while preserving precision.
Prototyping and 3D Printing
Rapid Prototyping Techniques: Rapid prototyping harnesses advanced 3D printing and additive manufacturing methods to swiftly and cost-effectively generate physical prototypes. These tangible representations of sheet metal parts enable hands-on assessment and testing for fit and functionality.
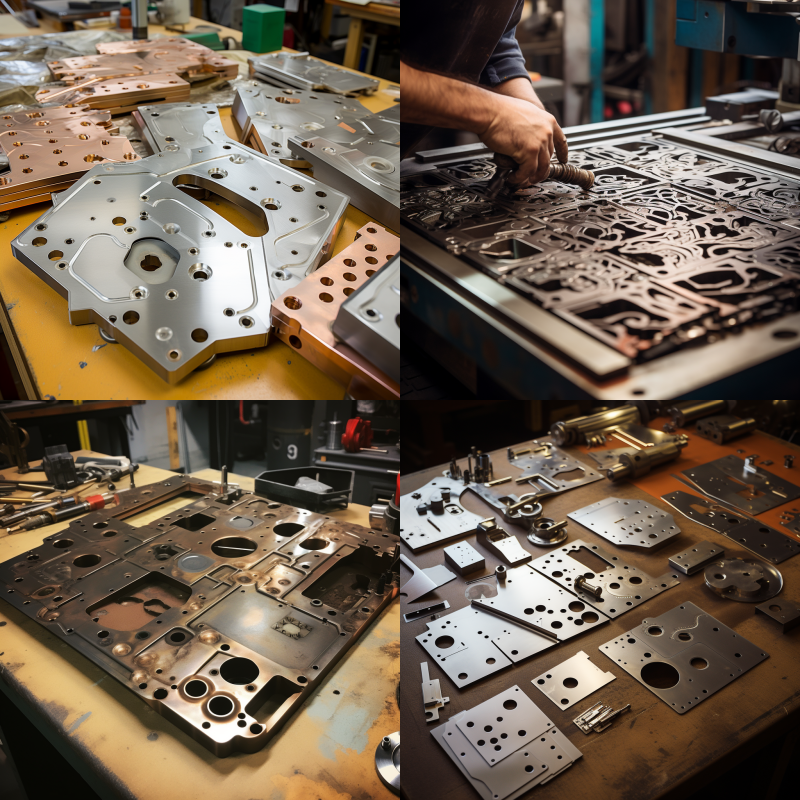
Benefits of Physical Prototypes: Physical prototypes confer practical advantages. They permit verification of dimensions, facilitate fit testing, and enable evaluation of assembly processes. These prototypes yield invaluable insights into real-world performance, facilitating early detection and resolution of issues during the development phase.
Tolerance Analysis and Precision Measurement
Utilization of Precision Measurement Equipment (Calipers, Micrometers): Employing precision measurement tools like calipers and micrometers ensures meticulous examination of sheet metal parts. These tools gauge dimensional accuracy, guaranteeing strict adherence to specified tolerances with exceptional precision.
Statistical Process Control (SPC): SPC harnesses statistical methodologies to monitor and govern production processes. It supports real-time data analysis, identifying trends, variations, and potential deviations from desired tolerances. SPC maintains manufacturing consistency while upholding high levels of accuracy.
Simulation Software for Bending and Forming
Virtual Bending and Forming Simulations: Specialized simulation software tailored for sheet metal bending and forming processes empowers engineers to create virtual models and assess the fabrication of intricate shapes. By simulating sheet metal deformation, it aids in refining designs and predicting potential accuracy-related challenges.
Ensuring Precision in Complex Shapes: Simulation software excels in evaluating and certifying the precision of intricate and elaborate sheet metal components. It aids in optimizing tooling and processes, minimizing material waste, and guaranteeing precision during the production of complex shapes.
Key Practices for Ensuring Sheet Metal Precision
Synergistic Design and Engineering Collaboration
Effective collaboration between design and engineering teams is paramount. Ensuring close coordination allows for a comprehensive grasp of design intent and functional requirements. This synergy helps identify potential challenges early in the process, enabling well-informed decisions that contribute to precision.
Meticulous Material Selection and Testing
Precise material selection is fundamental to achieving precision. Choosing the right material for a specific application is critical. Rigorous material testing, including tensile testing, hardness assessment, and material composition analysis, ensures that the selected material meets performance criteria and adheres to tolerances.
Robust Quality Control and Inspection Processes
Establishing rigorous quality control and inspection processes is essential. Regular inspections throughout production, utilizing tools like coordinate measuring machines (CMMs) and optical inspection systems, ensure that components adhere to stringent standards. This proactive approach identifies deviations and enables corrective measures.
Thorough Documentation and Record-Keeping
Comprehensive documentation and record-keeping are vital for traceability and accountability. Maintaining records of design iterations, material specifications, inspection results, and any modifications made during the proofing phase ensures transparency and facilitates problem-solving if issues arise during production.
Continuous Improvement and Feedback Loops
Implementing continuous improvement practices fosters an environment of innovation and excellence. Regular feedback loops among design, engineering, and production teams encourage the identification of opportunities for process enhancement. This iterative approach enhances efficiency and precision.
Strategies for Efficient and Effective Proofing
Streamlined Proofing Processes
Streamlining proofing processes reduces lead times and enhances efficiency. Leveraging digital tools for design validation, prototyping, and simulation accelerates the proofing phase. Additionally, automating routine tasks and workflows minimizes the potential for errors and expedites decision-making.
Scalability for Mass Production
Proofing isn’t solely about achieving precision on a small scale. It must consider the scalability of the production process. Ensuring that the methods and processes employed during proofing can seamlessly transition to mass production maintains precision across large volumes.
Cost-Effective Proofing Strategies
Cost-effectiveness is a critical consideration. While precision is paramount, it must be achieved without excessive cost escalation. Employing efficient material usage, optimizing tooling, and minimizing waste contribute to cost-effective proofing without compromising quality.
Staying Current with Industry Trends and Technology
The sheet metal fabrication industry continually evolves. Remaining updated on emerging technologies, materials, and methodologies is imperative. Investing in training and education for team members ensures that the latest advancements are integrated into the proofing process, enhancing precision and competitiveness.
Experience Precision Excellence with Louis Machine: Elevate Your Sheet Metal Parts Today!
In the realm of precision engineering, Louis Machine’s commitment to sheet metal parts proofing shines as a beacon of excellence. Our dedication to collaborative design, meticulous material selection, and rigorous quality control ensures that every component meets exacting standards. With a focus on continuous improvement and staying at the forefront of industry trends, Louis Machine exemplifies precision, delivering sheet metal parts that epitomize quality and reliability. In a world where precision matters, Louis Machine’s expertise continues to shape the future of sheet metal fabrication with unwavering precision and excellence.