Blog
We regularly update articles related to the prototyping and manufacturing industry. You’re welcome to check our previous blogs and subscribe to our newsletter.
A guide: What automotive parts are made with injection molding?
What automotive parts are made with injection molding?
Efficiency, accuracy, and innovation are the pillars of progress in the constantly changing world of car production. Injection molding is a vital technique that has transformed how automobile parts are made. Utilizing the strength of molten materials and precise molds, this process has become the mainstay of producing a vast array of automobile parts inside and outside the car.
Defining Comfort and Style in Interior Components:
You’ll discover a symphony of carefully designed interior elements inside each modern car, many of which were made possible via injection molding. What automotive parts are made with injection molding? This article discusses that Precision-made dashboard panels offer a pleasing balance of looks and utility. Drivers’ essential information is housed in instrument clusters, which are painstakingly shaped to guarantee smooth integration. The adaptability of injection molding is responsible for the user-friendly designs of center consoles with their storage compartments and controls. The ergonomic curves of seat components and the intricately textured door panels are just two examples of how injection molding is essential to producing cosy and aesthetically pleasing interior spaces. This technique is frequently used to shape the steering wheel, representing both tactile enjoyment and safety and providing the driver’s link to the road.
Exterior Elegance: Structural and Aesthetic Coherence:
Beyond the boundaries of the car, injection molding’s accuracy is also responsible for the external parts’ creation. Bumpers, a crucial component of impact absorption, have a strong structural design and perfectly capture the vehicle’s aesthetics. Grilles perfectly combine practicality and aesthetic appeal because of their distinctive shapes. Exterior door knobs are an underrated example of how elaborate but durable structures can be produced using injection molding. Side mirror housings, including sophisticated electrical components, are an excellent example of how technology and artistry coexist. While improving aerodynamics, wheel covers, and hubcaps are expertly made to endure the weather. Even the spoilers, which lend a touch of sportiness, show off how inventiveness and ingenuity are made possible by injection molding.
Increasing Efficiency using Injection Molded Automotive Parts:
For the production of numerous components and parts, the automobile industry uses the injection molding manufacturing technique extensively. To mould the material according to the intended design, molten material—typically plastic—is injected into a mold cavity throughout this process. The following details how injection molding improves the productivity of making car parts:
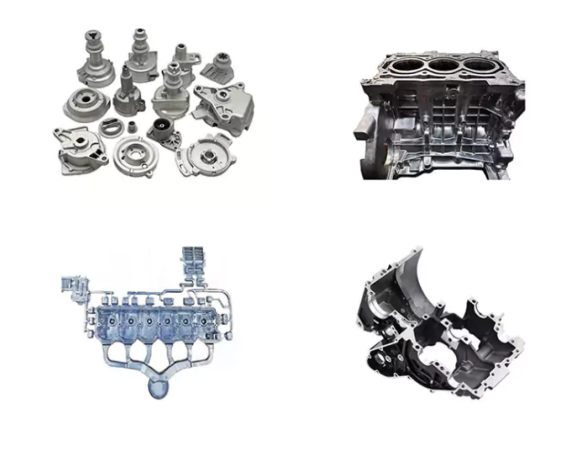
Mass manufacture:
Injection molding enables the quick and reliable manufacture of many vehicle parts. The procedure may be automated after the mold has been calibrated and set up, enhancing production rates and lowering labour costs.
Complex Geometries:
Using traditional manufacturing processes, producing elaborate and complex part geometries may take time and effort. However, the injection molding technique makes this possible. This is especially useful in the automobile sector, where parts frequently have complex forms and features for the best aesthetics and performance.
Material Efficiency:
By accurately regulating the amount of material injected into the mold, injection molding minimizes material waste. The capacity to recycle and reuse extra or damaged plastic material also lowers material costs and has a positive environmental impact.
- Consistency and Precision:
High dimensional precision and repeatability are ensured by injection molding, which is essential for automobile parts to fit together and operate as intended. This degree of uniformity lessens the need for tweaks and revisions after the fact.
- Reduced Assembly:
It is frequently possible to design injection-molded parts to include many functions, eliminating the requirement for separate parts and assembly stages. This improves the overall dependability of the parts while streamlining the production process and lowering the cost of assembly.
- Weight reduction:
To increase fuel economy and performance, automakers are always looking for methods to lighten the load on their cars. The design of strong yet lightweight components is made possible through injection molding, which helps reduce the vehicle’s total weight.
- Cost-effectiveness:
Due to the capacity to make parts in large quantities, decreased labour needs, minimum material waste, and faster production cycles, injection molding can result in cost savings.
- Material Options:
Elastomers, composites, and even metal-filled polymers are among the materials that injection molding can accommodate in addition to plastics. Due to their adaptability, producers may select materials that best meet the unique specifications of each vehicle item.
- Speed to Market:
Because automotive parts can be manufactured fast because of injection molding’s efficiency, it takes less time to introduce new car models or upgraded parts to the market.
- Customization and Innovation:
The simple integration of different design components, textures, and finishes is made possible through injection molding. This adaptability enables car designers to produce one-of-a-kind, cutting-edge components that satisfy both practical and aesthetic criteria.
What advantages come with utilizing Louis injection-molded car parts?
The automobile industry uses injection molding extensively to manufacture various parts and components. What automotive parts are made with injection molding? And the use of injection molding for automobile parts has various advantages:
Cost-Efficiency:
Producing large numbers of vehicle parts with injection molding is economical. The per-unit cost drops dramatically after the initial setup and tooling expenses are paid for, making mass manufacturing feasible.
High-Dimensional Accuracy and Precision:
Automotive parts produced by injection molding have these qualities. This is essential to ensuring that components fit together properly, enhancing the vehicle’s overall performance and safety.
Consistency and Reproducibility:
The automated nature of injection molding assures reproducibility and consistency in quality over a significant number of components. For the continued homogeneity and dependability of automobile components, this is essential.
Reduced Secondary Operations:
The amount of post-processing necessary for many injection-molded automobile parts is modest.
Conclusion:
Injection molding has completely changed how different parts and components are produced in the automobile industry. This manufacturing method has become a pillar of the automobile industry, producing anything from tiny delicate bits to massive structural components. In addition to precision mold design and production, plastic injection molding production, metal hardware parts processing production, and the manufacture of automobile components, we are a professional machining firm. LOUIS MACHINE can offer you a one-stop shop for design, manufacturing, injection molding or die-casting product production and processing bulk components thanks to our group of skilled technical members and managerial staff.